The Complete Guide to Construction Scheduling
Effective construction scheduling is a cornerstone of successful construction project management in the construction industry. From residential developments to large-scale infrastructure projects, having a detailed and actionable schedule ensures timely delivery, efficient resource allocation, and cost control. This guide dives deep into the essentials of construction scheduling, its methods, challenges, and tools, with a focus on practical tips and modern solutions.
What is Construction Scheduling?
Construction scheduling is the process of organizing and planning the activities, resources, and timelines needed to complete a construction project. It serves as a roadmap for stakeholders, helping to coordinate tasks and monitor progress throughout the project lifecycle. Construction schedules are vital for aligning expectations, preventing delays, and managing costs effectively.
Why is Construction Scheduling Crucial?
Construction scheduling plays a pivotal role in the successful delivery of projects. Here's why:
1. Time Management: It helps in allocating time for each activity, ensuring the project stays on track.
2. Resource Optimization: Efficiently plans the use of materials, labor, and equipment.
3. Cost Control: Prevents budget overruns by monitoring expenditures in line with the schedule.
4. Stakeholder Coordination: Aligns the efforts of sub-contractors, suppliers, and other parties.
5. Risk Mitigation: Identifies potential delays and provides solutions to keep the project moving.
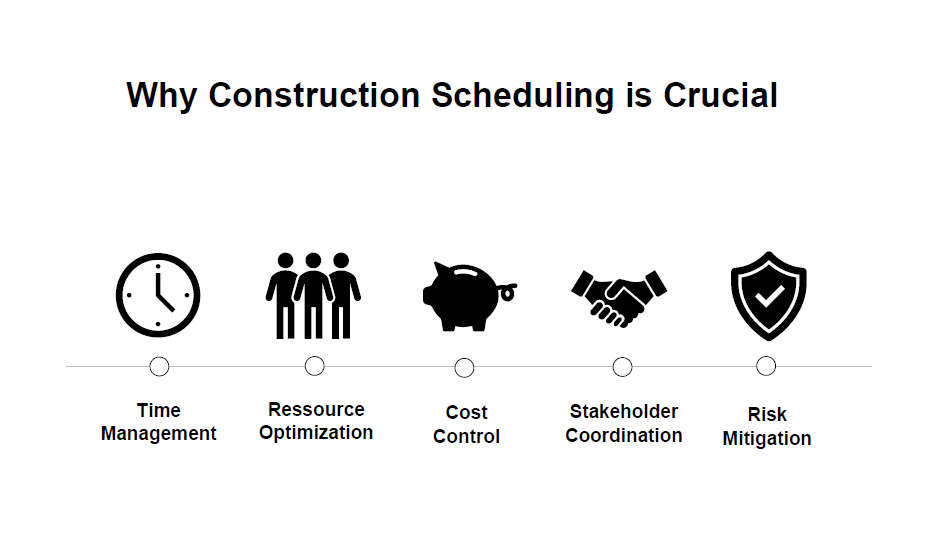
Key Elements of a Construction Schedule
1. Activities and Tasks
Clearly defined tasks ensure that every aspect of the project is accounted for.
2. Location-break down
Organizing tasks based on specific site locations ensures logical sequencing of work, reduces task overlap, and improves coordination between teams.
3. Durations
The durations for each task should be based on an estimate of the actual work to be done. It can be based either on the exact quantities of the building components under construction or rough assumptions provided by experienced workers.
4. Dependencies
Dependencies are crucial to define relationships between tasks, and enable fast setup and changing the schedule according to actual progress and on-site challenges
5. Resources and workforce
Efficient allocation of labor, materials, and equipment is essential for smooth operations.
6. Milestone and Deliverables
Breaking the project into key milestones helps measure success at various stages.
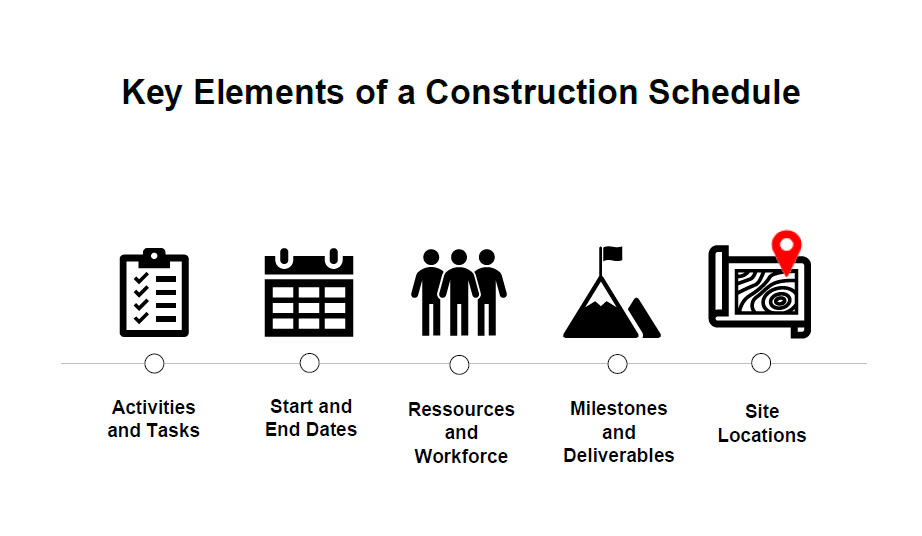
Popular Construction Scheduling Methods
Construction projects vary in complexity, and selecting the appropriate scheduling method is critical for success. Below are the most popular methods, each with its unique strengths.
Critical Path Method (CPM)
The Critical Path Method is one of the most widely used techniques in construction scheduling. It identifies the longest sequence of dependent tasks, known as the critical path, which dictates the minimum time needed to complete the project. Tasks on the critical path must be managed meticulously, as any delay directly impacts the project timeline. CPM is ideal for projects with clearly defined activities and dependencies, providing a structured approach to managing time-sensitive tasks. It is not suitable for construction where multiple crews or disciplines must share the space on-site.
Benefits:
• Provides a clear understanding of task priorities.
• Highlights dependencies and bottlenecks.
• Allows managers to allocate resources effectively.
Gantt Charts
Gantt charts are a visual scheduling tool that displays tasks against a timeline. Each task is represented as a horizontal bar, with its position and length indicating its start, duration, and end. These charts provide a comprehensive overview of the project and are particularly useful for tracking progress and identifying overlaps between tasks. The challenge with Gantt Charts is that they can become very long and difficult to overview for construction projects.
Benefits:
• Well known in construction.
• Ideal for smaller construction projects.
Program Evaluation and Review Technique (PERT)
PERT uses probabilistic time estimates (optimistic, pessimistic, and most likely durations) to schedule tasks. This method is especially usefulbeneficial for projects with a high degree of uncertainty or variability in task durations. By calculating expected task times and critical paths, PERT helps managers plan for the unexpected and manage risks proactively.
Benefits:
• Accommodates uncertainty in task durations.
• Enables more accurate risk assessments.
• Offers a statistical basis for scheduling decisions.
Last Planner System
The Last Planner System (LPS) is a lean construction methodology focused on improving workflow reliability. It emphasizes collaboration among all stakeholders, particularly subcontractors, to ensure that plans are realistic and achievable. LPS involves creating detailed short-term schedules and continuously revisiting plans to align with on-ground realities.
Benefits:
• Improves collaboration and accountability.
• Reduces waste and enhances efficiency.
• Promotes a more flexible and adaptive scheduling process.
Takt Time Planning
Takt Time Planning is a lean-based scheduling method that focuses on creating a consistent production rhythm across construction activities. It divides the project into zones or locations and aligns work tasks with a fixed time interval—called the takt time—to ensure steady progress.
Each crew moves from one zone to the next at the end of each takt, similar to an assembly line. TTP is particularly effective in projects with repetitive workflows and where multiple trades must coordinate work in shared spaces. Unlike CPM, it emphasizes flow, crew balance, and spatial coordination over detailed task dependencies.
Benefits:
• Promotes a smooth and predictable workflow.
• Improves collaboration and reduces downtime between trades.
• Helps identify and eliminate workflow interruptions early.
• Supports better use of space and resources on site.
Location-Based Scheduling
Location-Based Scheduling is similar to Takt Time Planning a highly effective approach to organizing construction tasks by aligning them with specific physical locations within the project. This method divides the project into clearly defined zones, aligning activities with their respective physical spaces. This spatial organization not only enhances clarity but also optimizes resource allocation, as teams can focus on completing work systematically in one area without interference from other tasks. The result is improved efficiency and smoother coordination, making location-based scheduling a valuable strategy for managing complex construction projects.
Benefits:
• Enhances clarity and reduces task conflicts.
• Facilitates better resource allocation across the site.
• Improves overall workflow and productivity.
Takt Time Planning and Location-Based Scheduling in Combination
Takt Time Planning and Location-Based Scheduling are a powerful combination for managing complex construction projects. Location-Based Scheduling uses project data—such as quantities, crew productivity, and location breakdowns—to generate accurate task durations and optimize resource use. When paired with Takt Time Planning’s fixed production rhythm, the result is a steady, balanced workflow across all project zones.
This hybrid approach leverages the strengths of both methods: the precision of data-driven planning and the collaborative rhythm of takt-based execution. It’s ideal for projects that require coordination between multiple crews working in shared spaces, and where predictability and flow are critical.
Benefits:
• Combines data-driven planning with flow-focused execution.
• Improves coordination between trades and across locations.
• Enhances predictability and reduces variability.
• Supports clear communication and steady progress on site.
These methods serve diverse project needs, and often, a combination of approaches yields the best results. Choosing the right proper method depends on the project size, complexity, and specific requirements. Integrating tools like Tactplan can further enhance these methods, ensuring efficiency and accuracy in execution. Link til Tactplan lbs
How to Create a Construction Scheduling Template
Effective construction scheduling requires a structured approach that integrates proven methodologies and principles, such as location-based scheduling and lean construction practices, including the Last Planner System. Below is an elaborated step-by-step guide to creating a robust construction scheduling template.
1. Define Project Objectives and Deliverables
Clearly outline the project's goals, scope, and expected outcomes to establish a solid foundation for your schedule. This ensures that all stakeholders are aligned on the vision and requirements from the outset, minimizing miscommunications and providing a clear direction for planning.
2. Break the Project into Tasks and Subtasks
Identify all activities required to complete the project, breaking them down into manageable components. This decomposition allows for detailed tracking of progress and ensures that every critical aspect of the project is accounted for.
3. Define locations
Organize tasks by specific site locations to streamline workflow and avoid conflicts between teams operating in the same area. This approach ensures that work in a given location is completed systematically before progressing to the next, improving efficiency and reducing delays. Combined with lean practices, location-based scheduling enhances workflow reliability and minimizes waste by aligning resources with physical spaces.
Example: By dividing a construction site into zones and sequencing activities logically, you can ensure that overlapping work is avoided, and each team has clear access to their designated area.
4. Assign Durations, Start/End Dates, and Dependencies
Set realistic timeframes for each task and establish relationships between activities to maintain a logical sequence. Incorporate lean construction principles here by engaging with all stakeholders, especially subcontractors, to ensure that these timelines are both practical and achievable. This step is where the Last Planner System is particularly valuable, as it emphasizes collaboration and commitment to realistic schedules.
5. Allocate Resources and Identify Constraints
Distribute labor, materials, and equipment efficiently while accounting for potential limitations or bottlenecks. Lean principles can guide this allocation by focusing on reducing waste and optimizing the use of available resources. By identifying constraints early, you can implement contingency measures that keep the project on track.
6. Incorporate Milestones and Checkpoints
Add key milestones to track progress and ensure alignment with project goals. These checkpoints serve as opportunities for teams to review performance, make adjustments, and reinforce lean principles of continuous improvement and accountability.
7. Incorporate the Last Planner System
The Last Planner System is a cornerstone of lean construction, focusing on engaging the people closest to the work in the planning process. Incorporate it into your template by including collaborative planning sessions, where subcontractors and site teams commit to tasks they can realistically achieve. This ensures higher reliability in task execution and promotes accountability across all levels of the project.
Steps to integrate Last Planner System:
• Conduct regular planning meetings to adjust the schedule based on on-ground realities.
• Use "pull planning" to sequence tasks, starting from the final deliverable and working backward. • Measure and track workflow reliability using metrics like Percent Plan Complete (PPC).
8. Review and Optimize the Schedule
Evaluate the schedule for potential improvements, resolve any conflicts, and incorporate feedback from stakeholders to finalize a realistic and actionable plan. Lean principles advocate for iterative reviews to identify inefficiencies, eliminate waste, and refine workflows. Use visualization tools to ensure that all stakeholders understand the schedule and can provide actionable insights. Strive for rhythmic production and continuous flow.
By following these steps, you can create a construction scheduling template that incorporates the latest best practices, including lean principles, the Last Planner System, and location-based scheduling. This comprehensive approach not only ensures efficient workflows but also promotes collaboration, accountability, and continuous improvement across all project phases.
Examples of Construction Scheduling Templates
You can download a simple Excel tool to try working with location-based scheduling here.
You can see an examples of a Construction Schedule here:
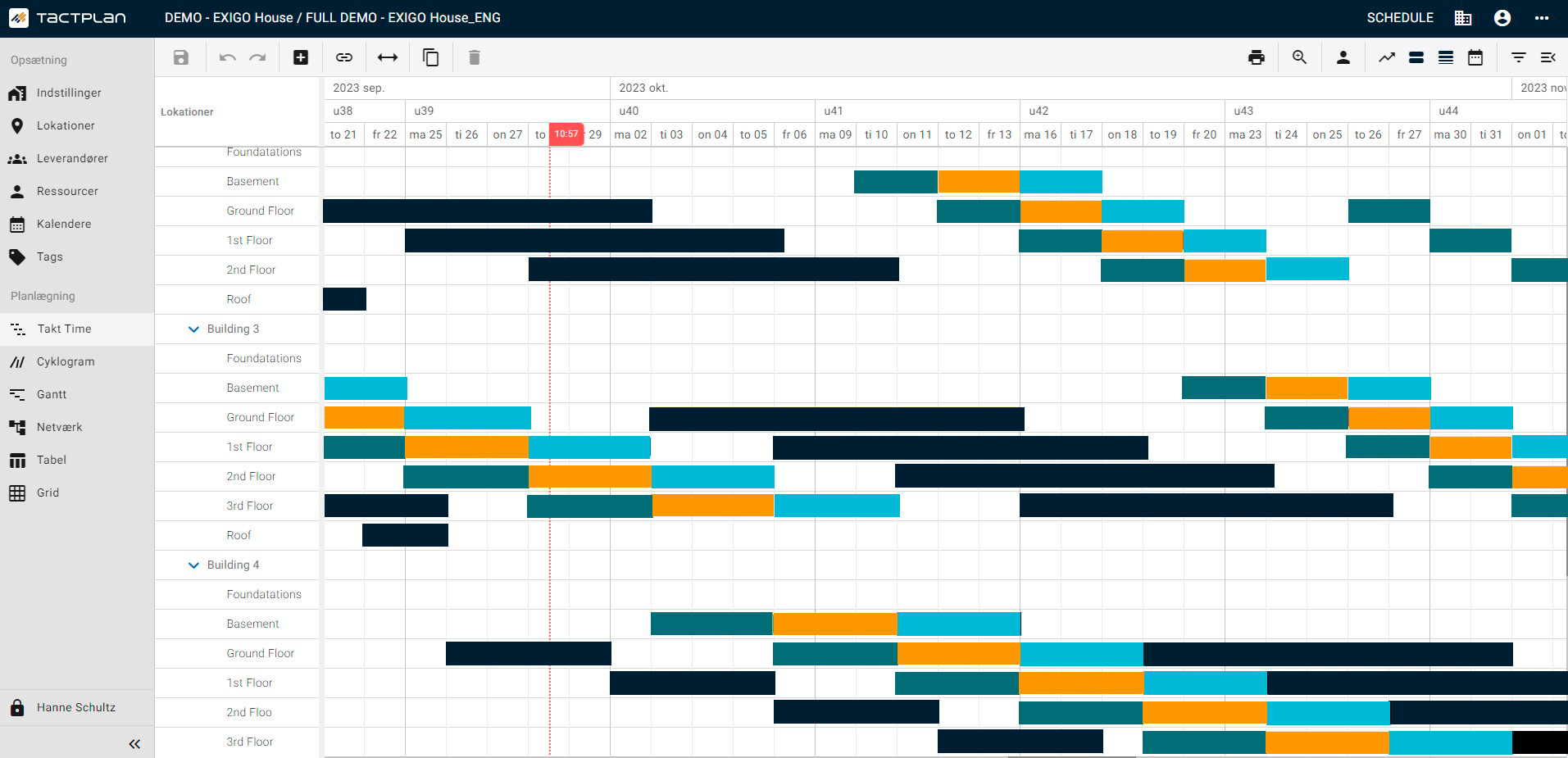
Best Practices for Effective Construction Scheduling
How Tools Like Tactplan Incorporate Research Findings
Modern tools, such as Tactplan, integrate both location-based scheduling and lean principles, making these research-backed methods accessible and practical for construction professionals. Features like real-time updates, spatial task visualization, and collaboration tools align with the latest research to deliver cutting-edge solutions.
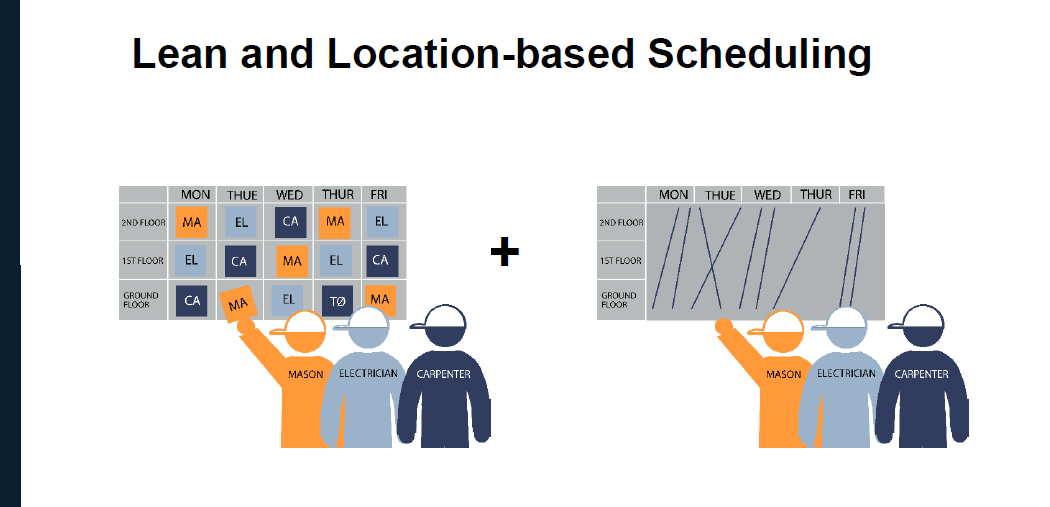
Key findings from a recent study include:
The research project "Improving Construction Labor Productivity and Efficiency in Renovation Projects" by Hasse Højgaard Neve offers several key insights:
1. Significance of On-Site Craftsmen's Efficiency:
The study emphasizes that the efficiency of on-site craftsmen—maximizing time spent on value-adding work (VAW) and minimizing non-value-adding work (NVAW)—is crucial for enhancing national-level construction labor productivity (CLP).
2. Identification of System Behaviors Affecting Time Utilization:
Five system behaviors were identified that influence how VAW and NVAW manifest in renovation projects. Understanding these behaviors provides insights into time wastage and areas for improvement.
3. Impact of Lean Construction Methods:
The research demonstrates that implementing lean construction methods positively affects VAW in renovation projects, leading to more efficient workflows and reduced waste.
These findings offer valuable guidance for policymakers and industry professionals aiming to enhance efficiency in construction renovation projects.
Learn more about Hasse Højgaard Neves findings here:
Best Practices for Effective Construction Scheduling
1. Early Engagement and Understanding the Method
Early and continuous engagement ensures that everyone understands their roles, responsibilities, and timelines. Equally crucial is a shared understanding of the scheduling method, enabling clarity, reducing confusion, and supporting effective project execution.
2. Use Specialized Tools
Modern construction projects demand advanced tools to manage complexity. Software tools like Tactplan can streamline scheduling, provide real-time updates, and optimize workflows. These tools not only enhance visibility but also improve communication among teams, ensuring alignment with the project’s timeline and its real-time progress.
3. Update Regularly
Construction schedules are dynamic and must be adapted to reflect real-time changes. Regular updates allow for quick adjustments in response to unexpected delays, resource shortages, or changes in project scope. Keeping the schedule current ensures that stakeholders remain informed and can make proactive decisions.
4. Incorporate Contingencies
No project is immune to delays or disruptions. Building buffer time into the schedule provides a safety net for unforeseen events, such as weather issues, material shortages, or labor conflicts. Contingency planning keeps the project on track even when challenges arise.
5. Leverage Location-Based Scheduling
Organizing tasks based on specific site locations is a highly effective practice, especially for large or complex projects. Location-based scheduling aligns activities with physical areas of the site, allowing teams to work systematically without overlapping tasks. This method ensures smoother transitions between work zones, reduces bottlenecks, and enhances resource allocation. Tools like Tactplan offer features tailored for location-based scheduling, providing clear visualizations of progress within each zone and enabling better coordination across teams.
6. Integrate Quality into Scheduling
Quality assurance should be an integral part of the scheduling process. Regular inspections, material checks, and adherence to industry standards help maintain high-quality deliverables without compromising timelines. Embedding quality checkpoints ensures that rework is minimized, enhancing both efficiency and outcomes.
Learnings from Hasse Neves studies:
7. Embrace Lean Principles and the Last Planner System
Lean construction principles focus on eliminating waste, enhancing efficiency, and improving collaboration across all project phases. The Last Planner System (LPS), a core component of lean construction, emphasizes realistic planning and commitment at all levels of the project. Hasse Neve's findings demonstrate that lean methods can significantly improve VAW by streamlining workflows and reducing inefficiencies.
8. Focus on On-Site Efficiency
Building on Hasse Neve's research, maximizing value-adding work (VAW) and minimizing non-value-adding work (NVAW) for on-site craftsmen is essential. Time management improvements at the ground level can significantly enhance overall construction labor productivity (CLP). Scheduling should account for these productivity dynamics to optimize on-site operations.
9. Identify and Address System Behaviors
According to Hasse Neve’s research, understanding and mitigating systemic behaviors that influence VAW and NVAW is critical in renovation projects. By recognizing these behaviors early, project managers can implement targeted strategies to reduce time wastage and improve scheduling outcomes.
Incorporating these practices, construction scheduling becomes a more robust, dynamic, and efficient process, ensuring project success while aligning with the latest industry research and methodologies.
Common Challenges in Construction Scheduling and How to Overcome Them
Challenges
1. Resource Conflicts
In traditional scheduling, conflicts often arise when multiple contractors are assigned to the same location at the same time, causing delays, overcrowding, and decreased productivity.
2. Underutilized Areas on the Construction Site
Poor planning can lead to certain zones of the construction site remaining unused while other areas experience congestion. This inefficiency not only wastes valuable space but can also result in delays as resources are not distributed effectively across the site.
3. Uneven Flow of Activities
A lack of synchronization between tasks can cause downtime for contractors, leaving workers waiting for preceding activities to be completed. This uneven flow disrupts productivity and often leads to extended project timelines and increased costs.
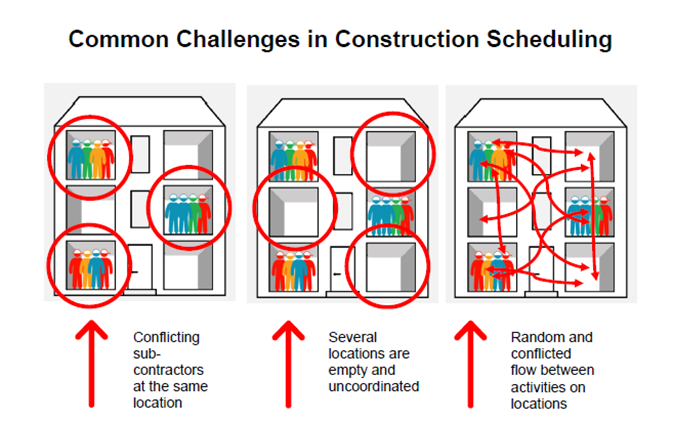
How to Overcome These Challenges
1. Resolve Resource Conflicts with Location-Based Scheduling
- Use tools like Tactplan to align tasks with specific physical zones, ensuring contractors are not scheduled in the same area simultaneously.
- Regularly review and adjust schedules to prevent overlaps and optimize space utilization.
2. Optimize Site Utilization through Strategic Planning
- Break the site into well-defined zones and allocate resources systematically.
- Employ real-time updates from scheduling tools to ensure even resource distribution and avoid congestion.
3. Ensure an Even Flow of Activities with Better Synchronization
- Use lean principles such as Location-based Scheduling and the Last Planner System to collaboratively plan workflows and reduce idle time.
- Conduct regular progress reviews and adjust schedules dynamically to address bottlenecks or delays.
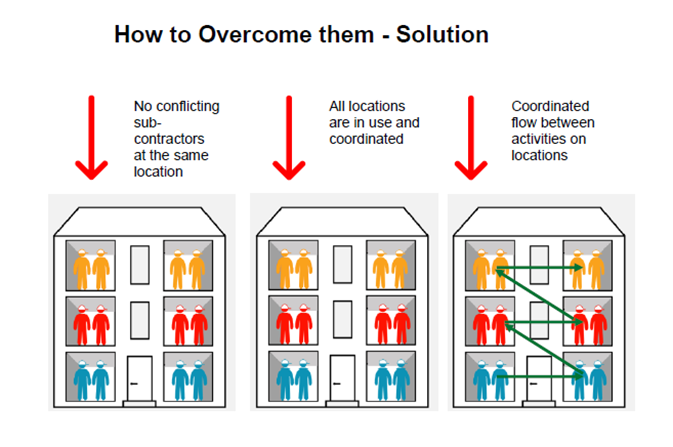
The Role of Construction Managers in Scheduling
Construction managers play a pivotal role in ensuring the smooth execution of construction projects, and scheduling is a core aspect of their responsibilities. Their ability to manage time, resources, and workflows effectively is critical to achieving project objectives. Drawing on the principles of construction management and building informatics, their role in scheduling extends beyond traditional planning to embrace advanced technologies and collaborative approaches.
Key Responsibilities in Scheduling
1. Developing Comprehensive Schedules
- Construction managers are tasked with creating detailed project schedules that outline all activities, dependencies, and milestones.
- They use advanced tools, such as location-based scheduling and the Critical Path Method (CPM), to ensure accuracy and optimize timelines.
2. Integrating Building Informatics
- Leveraging data and digital models, such as Building Information Modeling (BIM), construction managers can create dynamic schedules that adapt to real-time changes.
- These technologies enable precise planning of tasks, resource allocation, and risk management.
3. Facilitating Collaboration Among Stakeholders
- Construction managers act as a bridge between architects, engineers, contractors, and clients.
- Through effective communication, they ensure that all parties understand the schedule and are aligned on timelines and expectations.
4. Monitoring Progress and Adjusting Schedules
- Real-time monitoring of progress allows construction managers to identify delays or issues quickly.
- They proactively adjust schedules to accommodate changes, such as unexpected site conditions or resource shortages, ensuring the project stays on track.
5. Implementing Risk Management Strategies
- By incorporating contingency plans, construction managers prepare for potential disruptions, such as weather delays or supply chain issues.
- They ensure that these risks are mitigated within the scheduling process to avoid major setbacks.
6. Optimizing Resource Utilization
- Construction managers allocate labor, materials, and equipment efficiently, ensuring resources are neither overburdened nor underutilized.
- They use scheduling tools to streamline workflows and eliminate bottlenecks.
Skills Required for Effective Scheduling
Construction managers need a combination of technical and managerial skills, including:
• Technical Proficiency: Knowledge of scheduling methodologies like LBMS, CPM, Gantt charts, and lean principles.
• Digital Competence: Expertise in tools such as BIM, Tactplan, and other construction management software.
• Analytical Thinking: Ability to assess complex data and foresee scheduling conflicts or delays.
• Leadership and Communication: Skills to manage diverse teams and ensure alignment among all stakeholders.
Embracing Advanced Technologies
Modern construction managers integrate innovative technologies into their scheduling practices. Tools like BIM and real-time scheduling platforms provide a holistic view of project progress, enhance decision-making, and improve coordination across teams.
By combining technical expertise, collaborative management, and digital tools, construction managers ensure that schedules are realistic, efficient, and adaptable to the dynamic nature of construction projects. Their role is central to delivering projects on time, within budget, and to the highest quality standards.
Tools and Software for Construction Scheduling
The advent of modern construction scheduling tools has significantly enhanced how projects are planned and executed. Among these tools, Tactplan stands out as a game-changer, offering a suite of advanced features tailored to meet the dynamic needs of construction professionals.
Key Features of locationbased scheduling and Tactplan
We asked users of location-based scheduling to share their experiences and insights, and these are the key features they identified as most valuable in their construction projects. These features highlight what users say makes the biggest difference in improving efficiency, collaboration, and overall project success:
1. Enhanced Planning Accuracy
Tactplan leverages location-based scheduling to create precise and dynamic project timelines, improving control over the construction process and minimizing delays.
2. Optimized Resource Utilization
By aligning tasks with specific locations, Tactplan enables efficient resource use, reducing downtime and lowering project costs.
3. Improved Collaboration Among Teams
Detailed scheduling fosters better communication and teamwork among various disciplines, minimizing misunderstandings and enhancing project flow.
4. Increased Flexibility for Changes
With location-based planning, Tactplan allows for rapid adjustments to staffing and tasks in response to unforeseen events, ensuring project continuity.
5. Higher Employee Engagement
Clear and accessible plans make it easier for workers to follow schedules and take responsibility, boosting their commitment and accountability.
6. Enhanced Communication with Clients
Location-focused scheduling strengthens communication with clients, providing them with greater insight into the construction process and increasing their confidence.
7. Optimized Logistics Management
By focusing on specific locations, Tactplan ensures materials and equipment are available when needed, reducing wait times and costs.
8. Effective Timeline Management
Tactplan enables efficient monitoring and adjustment of project timelines, allowing for quick adaptations to changes and maintaining overall progress.
9. Ensured Construction Quality
A structured approach to scheduling helps maintain high work quality, reducing the need for repairs or modifications later in the process.
These features reflect what users value most in Tactplan, showcasing its ability to deliver practical, real-world benefits for construction projects.
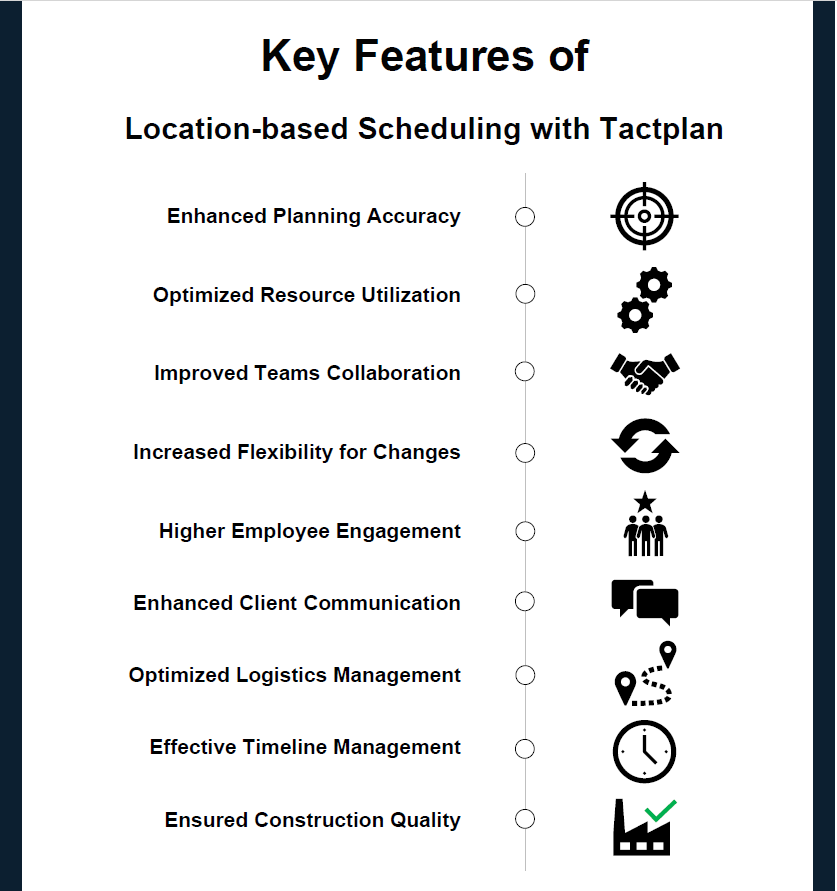
Why Tactplan
Tactplan stands out as an essential tool for construction managers, shaped by the real-world experiences of its users. With features like location-based scheduling, resource optimization, and real-time adaptability, Tactplan directly addresses the industry's biggest challenges.
Users praise its ability to enhance planning accuracy, foster collaboration, and provide flexibility for unexpected changes. From small residential projects to complex infrastructure builds, Tactplan empowers teams to streamline workflows, improve communication, and deliver exceptional results while maintaining quality and staying on schedule.
Conclusion
Effective construction scheduling is the backbone of successful project management, enabling teams to deliver on time, within budget, and to the highest standards. This guide has explored the essential aspects of construction scheduling, from its methods and challenges to best practices and advanced tools like Tactplan.
What truly sets construction scheduling apart is its ability to align diverse stakeholders, optimize resources, and adapt to dynamic project conditions. Tools like Tactplan, designed with input from real users, exemplify the power of modern, location-based scheduling to tackle industry challenges, foster collaboration, and ensure precision at every stage of a project.
As construction projects grow increasingly complex, the importance of embracing innovative approaches and technologies cannot be overstated. By integrating proven methodologies such as the Critical Path Method, lean principles, and location-based scheduling, professionals can set their projects up for success. With the right strategies and tools in place, construction managers can confidently navigate the challenges of the industry and achieve outstanding results.
By embracing advanced tools like Tactplan, construction professionals can:
1. Enhance Planning Precision
Create detailed and accurate schedules that minimize delays and improve overall project control.
2. Optimize Resource Utilization
Allocate labor, materials, and equipment effectively to reduce downtime and project costs.
3. Improve Collaboration Across Teams
Foster seamless communication and teamwork among diverse stakeholders, reducing misunderstandings and improving workflow.
4. Adapt Quickly to Changes
Adjust schedules in real-time to address unexpected disruptions, ensuring continuity and maintaining project timelines.
5. Boost Worker Engagement
Provide clear, actionable plans that empower workers to take ownership of their responsibilities and stay committed to project goals.
6. Streamline Client Communication
Offer clients greater transparency and insight into the construction process, building trust and confidence.
7. Optimize Logistics
Ensure materials and equipment are available when and where they are needed, minimizing wait times and enhancing efficiency.
8. Maintain High Quality Standards
Integrate structured planning approaches that reduce rework and uphold quality throughout the construction process.
9. Manage Timelines Effectively
Monitor and adjust schedules dynamically, keeping projects on track even in complex, fast-changing environments.
Ready to take your scheduling to the next level?Book a free online session with us – we’ll walk you through how Tactplan can improve your construction process with location-based planning.👉 Book your free demo and consultation